Two Component Structural silicone sealants are high in strength, capable of bearing large loads, and resistant to aging, fatigue, and corrosion, and have stable performance within the expected lifespan. They are suitable for adhesives that withstand the bonding of structural parts. It is mainly used for bonding metal, ceramics, plastics, rubber, wood and other materials of the same kind or between different kinds of materials, and can partially replace traditional connection forms such as welding, riveting and bolting.
Silicone structural sealant is a key material used in fully hidden or semi-hidden frame glass curtain walls. By connecting the plates and metal frames, it can withstand wind loads and glass self-weight loads, which is directly related to the durability and safety of building curtain wall structures. One of the key links of glass curtain wall safety.
It is a structural sealant with linear polysiloxane as the main raw material. During the curing process, the crosslinking agent reacts with the base polymer to form an elastic material with a three-dimensional network structure.Because the Si-O bond energy in the molecular structure of silicone rubber is relatively large in common chemical bonds (Si-O specific physical and chemical properties: bond length 0.164±0.003nm, thermal dissociation energy 460.5J/mol. Significantly higher than C-O358J/mol, C-C304J/mol, Si-C318.2J/mol), compared with other sealants (such as polyurethane, acrylic, polysulfide sealant, etc.), UV resistance and resistance The atmospheric aging ability is strong, and it can maintain no cracks and deterioration for 30 years in various weather environments. It has ±50% resistance to deformation and displacement in a wide temperature range. However, with the increase in the use of silicone structural sealants, various problems will appear in practical applications, such as: particle agglomeration and pulverization of component B, segregation and stratification of component B, compression The plate cannot be pressed down or the glue is turned over, the glue output speed of the glue machine is slow, the glue of the butterfly sheet has particles, the surface drying time is too fast or too slow, the glue appears skinning or vulcanization, and "flower glue" appears during the glue making process. ", the colloid cannot be cured normally, sticky hands after a few days of curing, the hardness is abnormal after curing, there are needle-like pores on the bonding surface with the substrate, air bubbles are trapped in the silicone sealant, poor bonding with the substrate, incompatibility with accessories, etc.
2.FAQ analysis of Two Component Structure silicone adhesive
2.1 B part has particle agglomeration and pulverization
If the particle agglomeration and pulverization of component B occurs, there are two reasons: one is that this phenomenon has occurred in the upper layer before use, which is due to poor sealing of the package, and the cross-linking agent or coupling agent in component B is Active compound, susceptible to moisture in the air, this batch should be returned to the manufacturer. The second is that the machine is shut down during use, and the particle agglomeration and pulverization occurs when the machine is turned on again, indicating that the seal between the pressure plate of the glue machine and the rubber material is not good, and the equipment should be contacted to solve the problem.
2.2 The speed of the glue machine is slow
When the product is used for the first time, the glue output speed of the gluing machine is too slow during the gluing process. There are three possible reasons: ⑴ component A has poor fluidity, ⑵ the pressure plate is too large, and ⑶ the air source pressure is not enough.
When it is determined that it is the first reason or the third reason, we can solve it by adjusting the pressure of the glue gun; when it is determined that it is the second reason, ordering a barrel with a matching caliber can solve the problem. If the glue output speed slows down during normal use, it may be that the mixing core and the filter screen are blocked. Once found, the equipment needs to be cleaned in time.
2.3 Pull-off time is too fast or too slow
The breaking time of the structural adhesive refers to the time it takes for the colloid to change from a paste to an elastic body after mixing, and it is generally tested every 5 minutes. There are three factors affecting the drying and curing of the rubber surface: (1) the influence of the proportion of A and B components, etc.; (2) temperature and humidity (the influence of temperature is the main one); (3) the formula of the product itself is defective.
The solution to the reason (1) is to adjust the ratio. Increasing the proportion of component B can shorten the curing time and make the adhesive layer hard and brittle; while reducing the proportion of curing agent will prolong the curing time, the adhesive layer will become softer, the toughness will be enhanced and the strength will be increased. reduce.
Generally, the volume ratio of component A:B can be adjusted between (9~13:1). If the proportion of component B is high, the reaction speed will be faster and the breaking time will be shorter. If the reaction is too fast, the time for trimming and stopping the gun will be affected. If it is too slow, it will affect the drying time of the colloid. The breaking time is generally adjusted between 20 and 60 minutes. The performance of the colloid after curing in this ratio range is basically the same. In addition, when the construction temperature is too high or too low, we can appropriately reduce or increase the proportion of component B (curing agent), so as to achieve the purpose of adjusting the surface drying and curing time of the colloid. If there is a problem with the product itself, the product needs to be replaced.
2.4 "Flower glue" appears in the process of gluing
The flower gum is produced due to the uneven mixing of the colloids of the A/B components, and it appears as a local white streak. The main reasons are: ⑴The pipeline of component B of the glue machine is blocked; ⑵The static mixer has not been cleaned for a long time; ⑶The scale is loose and the glue output speed is uneven; It can be solved by cleaning the equipment; for the reason (3), you need to check the proportional controller and make appropriate adjustments.
2.5 Skinning or vulcanization of the colloid during the glue making process
When the two-component adhesive is partially cured during the mixing process, the glue produced by the glue gun will appear skinning or vulcanization. When there is no abnormality in the curing and glue-out speed, but the glue is still crusted or vulcanized, it may be that the equipment has been shut down for a long time, the glue gun has not been cleaned or the gun is not cleaned thoroughly, and the crust or vulcanized glue needs to be rinsed. Construction after cleaning.
2.6 There are air bubbles in the silicone sealant
Generally speaking, the colloid itself has no air bubbles, and the air bubbles in the colloid are likely to be mixed with air during transportation or construction, such as: ⑴The exhaust is not cleaned when the rubber barrel is replaced; ⑵The components are pressed on the plate after being put on the machine Not pressed down, resulting in incomplete defoaming. Therefore, the foam should be thoroughly removed before use, and the glue machine should be operated correctly during use to ensure sealing and prevent air from entering.
2.7 Poor adhesion to substrate
Sealant is not a universal adhesive, so it cannot be guaranteed to bond well with all substrates in practical applications. With the diversification of substrate surface treatment methods and new processes, the bonding speed and bonding effect of sealants and substrates are also different.
There are three forms of damage to the bonding interface between the structural adhesive and the substrate. One is cohesive damage, that is, cohesive force > cohesive force; the other is bond damage, that is, cohesive force < cohesive force. A junction damage area of less than or equal to 20% is qualified, and a bond damage area exceeding 20% is unqualified; a bond damage area exceeding 20% is an undesirable phenomenon in practical applications. There may be the following six reasons why the structural adhesive does not stick to the substrate:
⑴ The substrate itself is difficult to bond, such as PP and PE. Due to their high molecular crystallinity and low surface tension, they cannot form molecular chain diffusion and entanglement with most substances, so they cannot form a strong bond at the interface. Adhesion;
⑵ The bonding range of the product is narrow, and it can only work on some substrates;
⑶ maintenance time is not enough. Usually, the two-component structural adhesive should be cured for at least 3 days, while the single-component adhesive should be cured for 7 days. If the temperature and humidity of the curing environment are low, the curing time should be extended.
⑷ The ratio of components A and B is wrong. When using two-component products, the user must strictly follow the ratio required by the manufacturer to adjust the ratio of base glue and curing agent, otherwise problems may occur in the early stage of curing, or in the later stage of use in terms of adhesion, weather resistance and durability. question;
⑸ Failure to clean the substrate as required. Since the dust, dirt and impurities on the surface of the substrate will hinder the bonding, it should be cleaned strictly before use to ensure that the structural adhesive and the substrate are well bonded.
⑹ Failure to apply primer as required. The primer is used for pretreatment on the surface of the aluminum profile, which can improve the water resistance and durability of the bond while shortening the bonding time. Therefore, in actual engineering applications, we must use the primer correctly and strictly avoid degumming caused by improper use methods.
2.8 Incompatibility with accessories
The reason for the incompatibility with the accessories is that the sealant has a physical or chemical reaction with the accessories in contact, resulting in hazards such as discoloration of the structural adhesive, non-stick to the substrate, degradation of the performance of the structural adhesive, and shortened life of the structural adhesive.
3. Conclusion
Silicone structural adhesive has high strength, high stability, excellent aging resistance, high temperature resistance and other excellent properties, and is widely used in the structural bonding of building curtain walls. However, in practical applications, due to human factors and the problems of the selected base material (the construction specifications cannot be strictly followed), the performance of the structural adhesive is greatly affected, and even made invalid. Therefore, the compatibility test and adhesion test of glass, aluminum materials and accessories should be checked before construction, and the requirements of each link should be strictly followed during the construction process, so as to achieve the effect of structural adhesive and ensure the quality of the project.
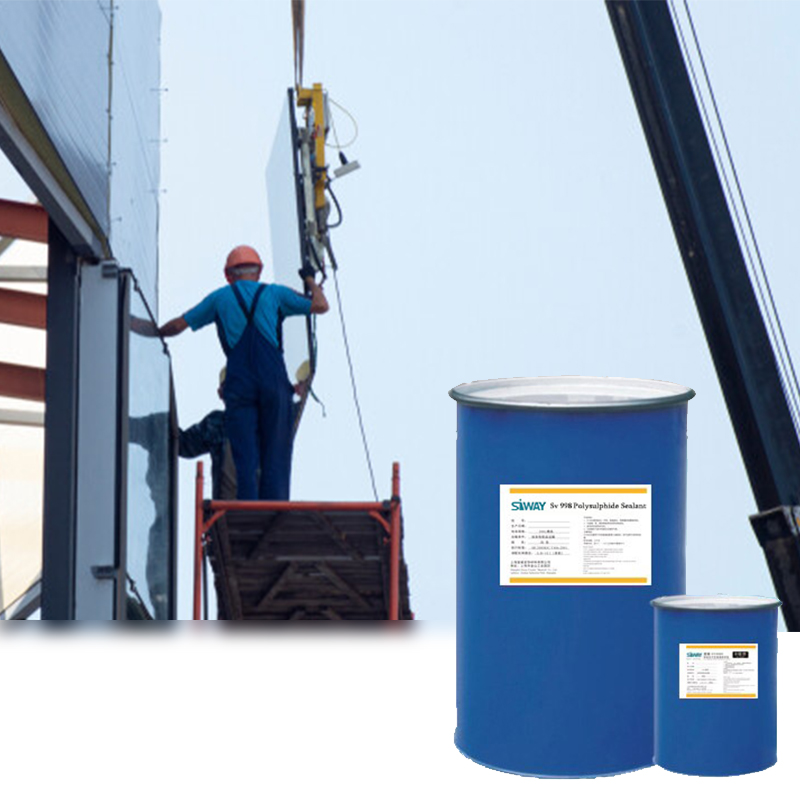
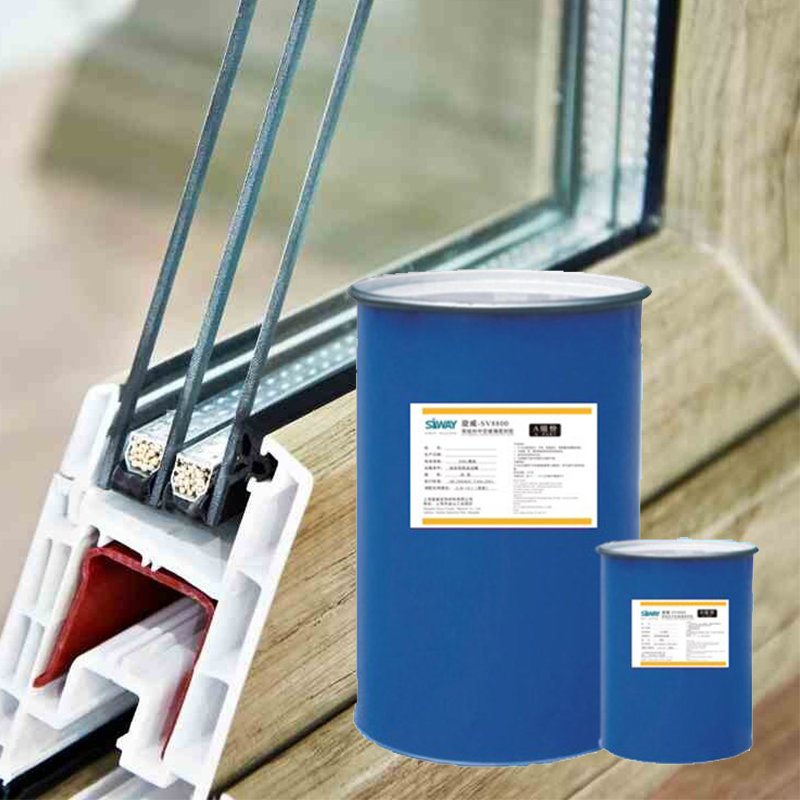
Post time: Nov-30-2022